Material Research
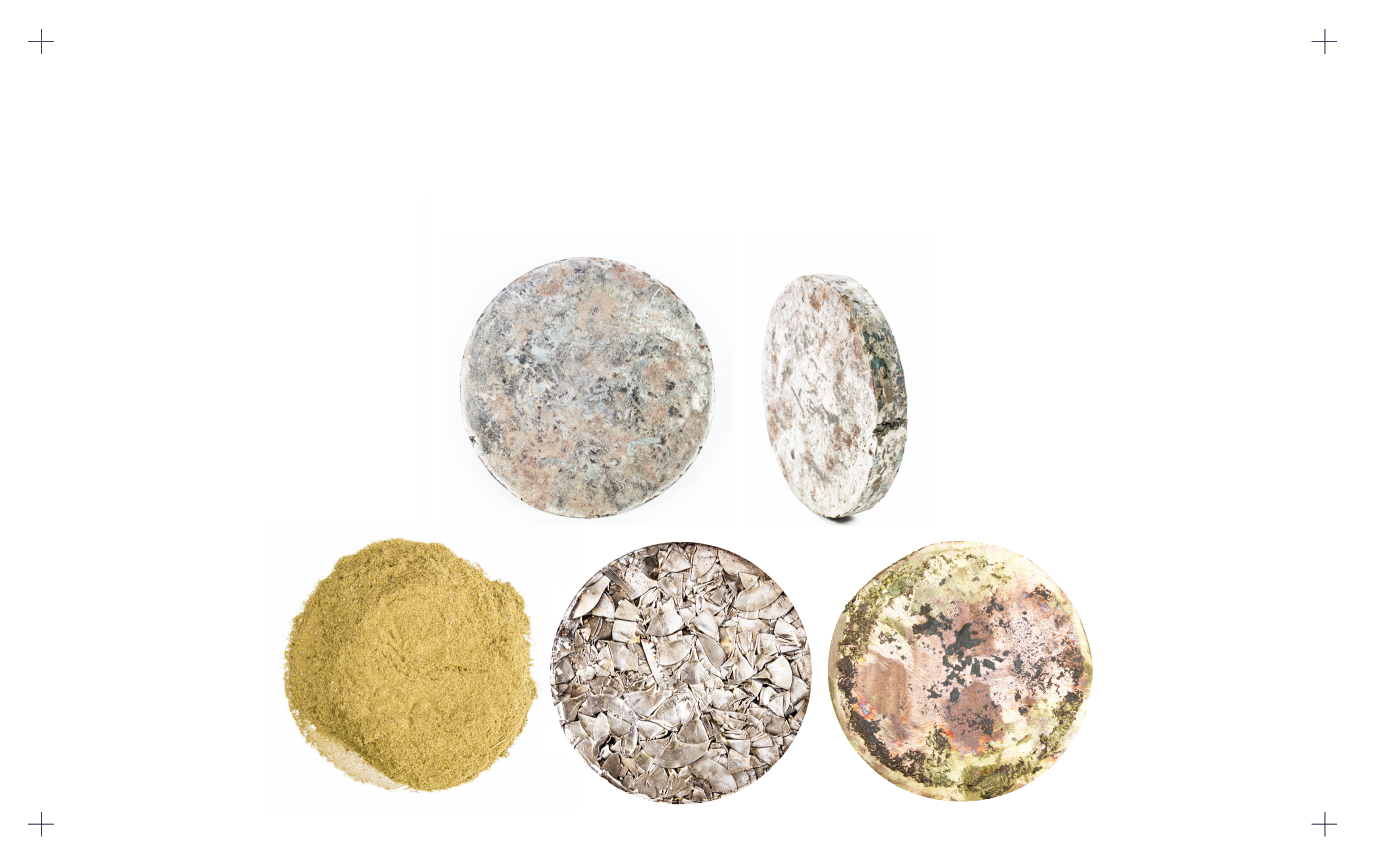
The Value
Of Industrial
Waste Materials
PROJECT
EXPLORING THE VALUE OF INDUSTRIAL WASTE MATERIALS AND CREATING SUSTAINABLE PRACTISES IN INDIA
SECTOR
SUSTAINABILITY
ORGANISATION
GODREJ INNOVATION CENTER
ROLE
MATERIAL RESEARCH & COMMUNICATION
WORKSHOP DURATION
1 YEAR 2 MONTHS
EXPLORING THE VALUE OF INDUSTRIAL WASTE MATERIALS AND CREATING SUSTAINABLE PRACTISES IN INDIA
SECTOR
SUSTAINABILITY
ORGANISATION
GODREJ INNOVATION CENTER
ROLE
MATERIAL RESEARCH & COMMUNICATION
WORKSHOP DURATION
1 YEAR 2 MONTHS
The Punah Project focused on building awareness around the importance of industrial waste materials and their value as a resource. At Godrej and Boyce, one of India’s largest manufacturing companies, 18,505 tonnes of industrial waste materials are generated during the manufacturing process every year. Large quantities of materials that are resource, production and energy intensive to be manufactured in the first place, are down-cycled, sent to incineration or landfill.
Our objective centered around building a rigorously categorised repository of waste to ensure access to waste materials and creating a blueprint of ways in which to recycle materials and create closed-loop systems.
KEY METHODOLOGIES & TOOLS
MATERIAL RESEARCH
DOCUMENTATION OF WASTE STREAMS
COMMUNICATION DESIGN
WORKSHOP FACILITATION
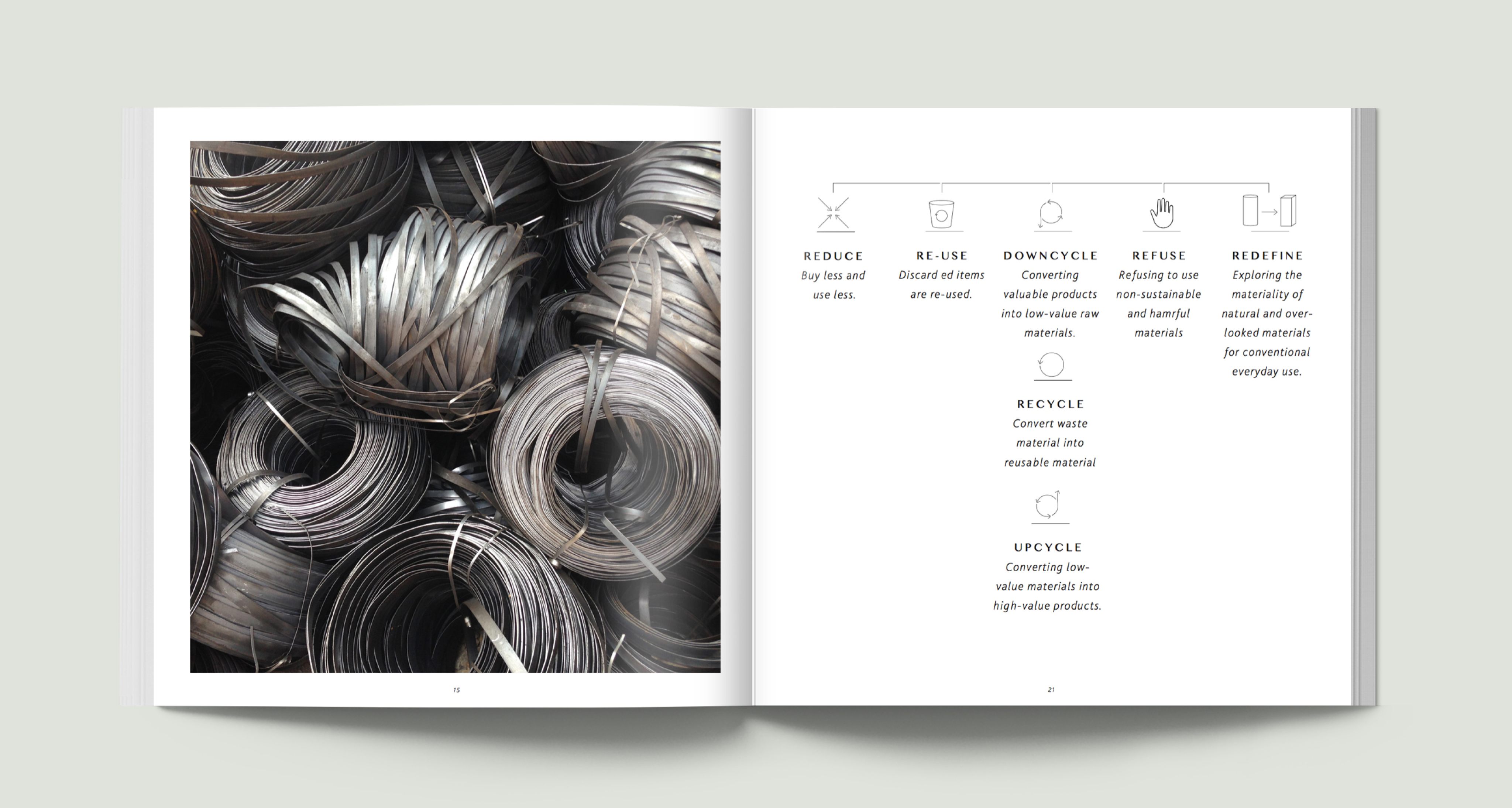
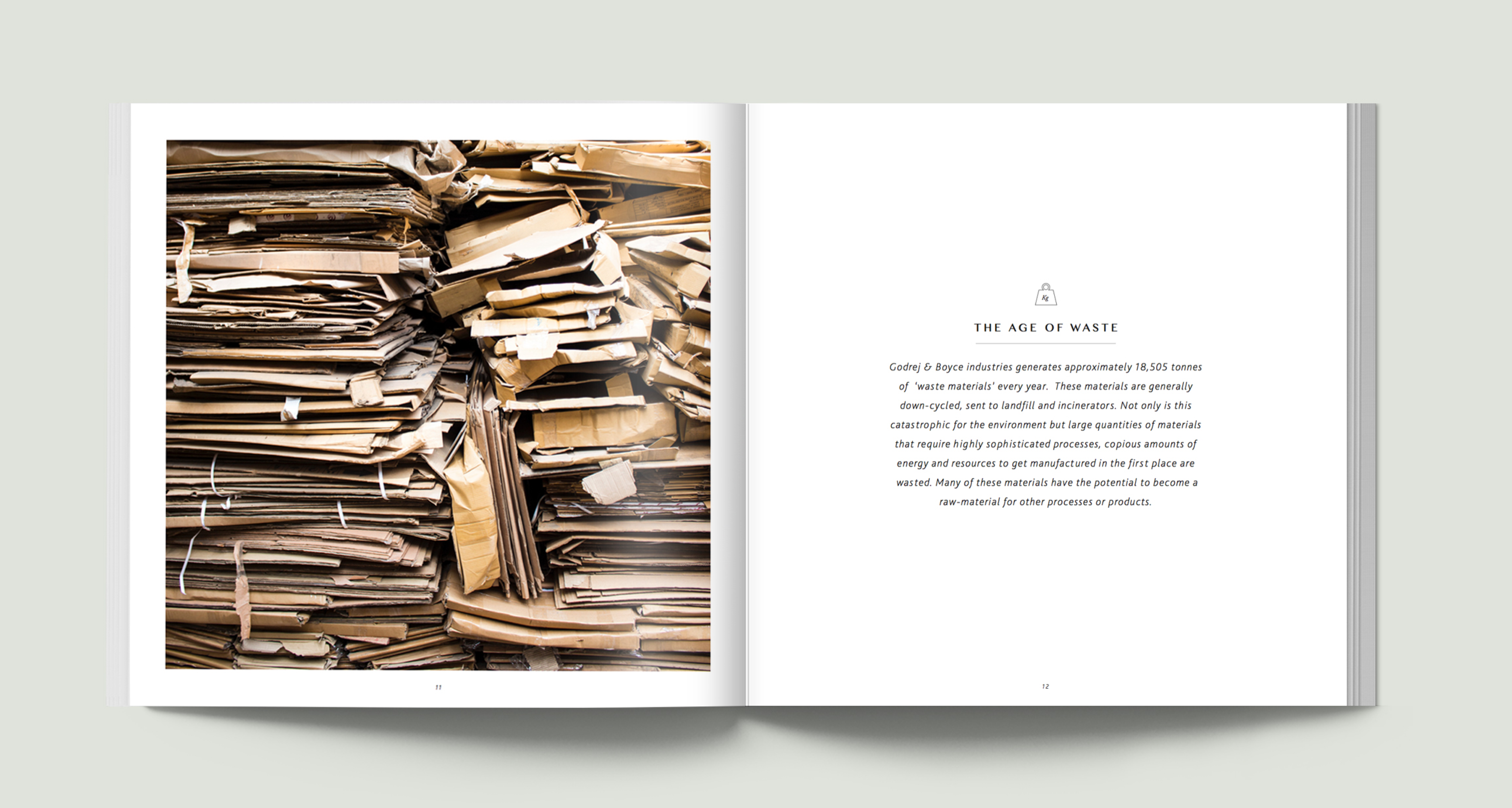
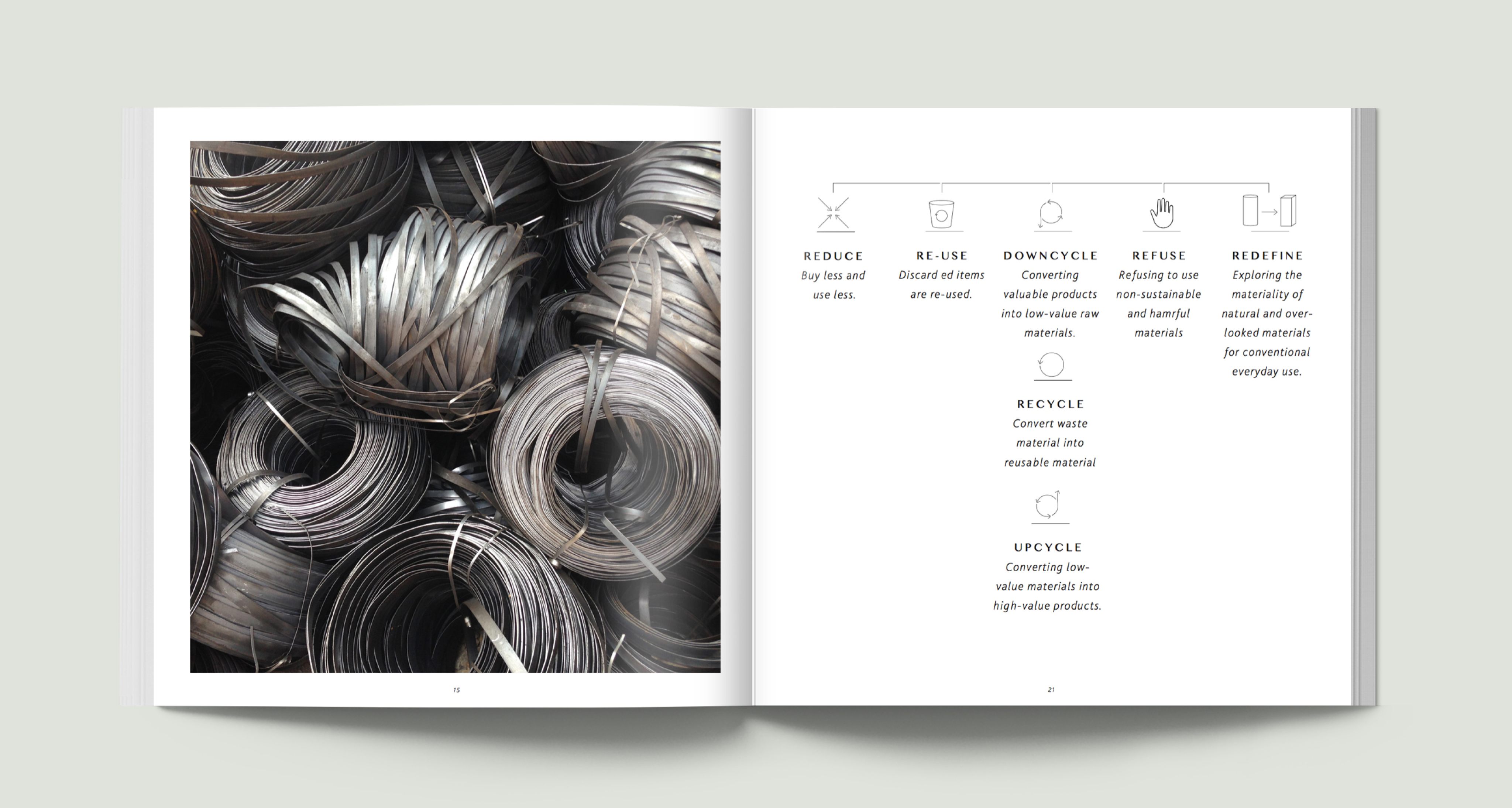


01
Mapping Waste Streams
We mapped out waste streams, collecting and recording data on more than 700+ waste materials generated during manufacturing.
02
Documenting Waste Samples
We documented properties, quantities of waste generated per month, the respective manufacturing process and waste stream journeys.
03
Building a Waste Repository
We collated the data and categorized all waste materials according to properties and type in order to create a waste material repository.
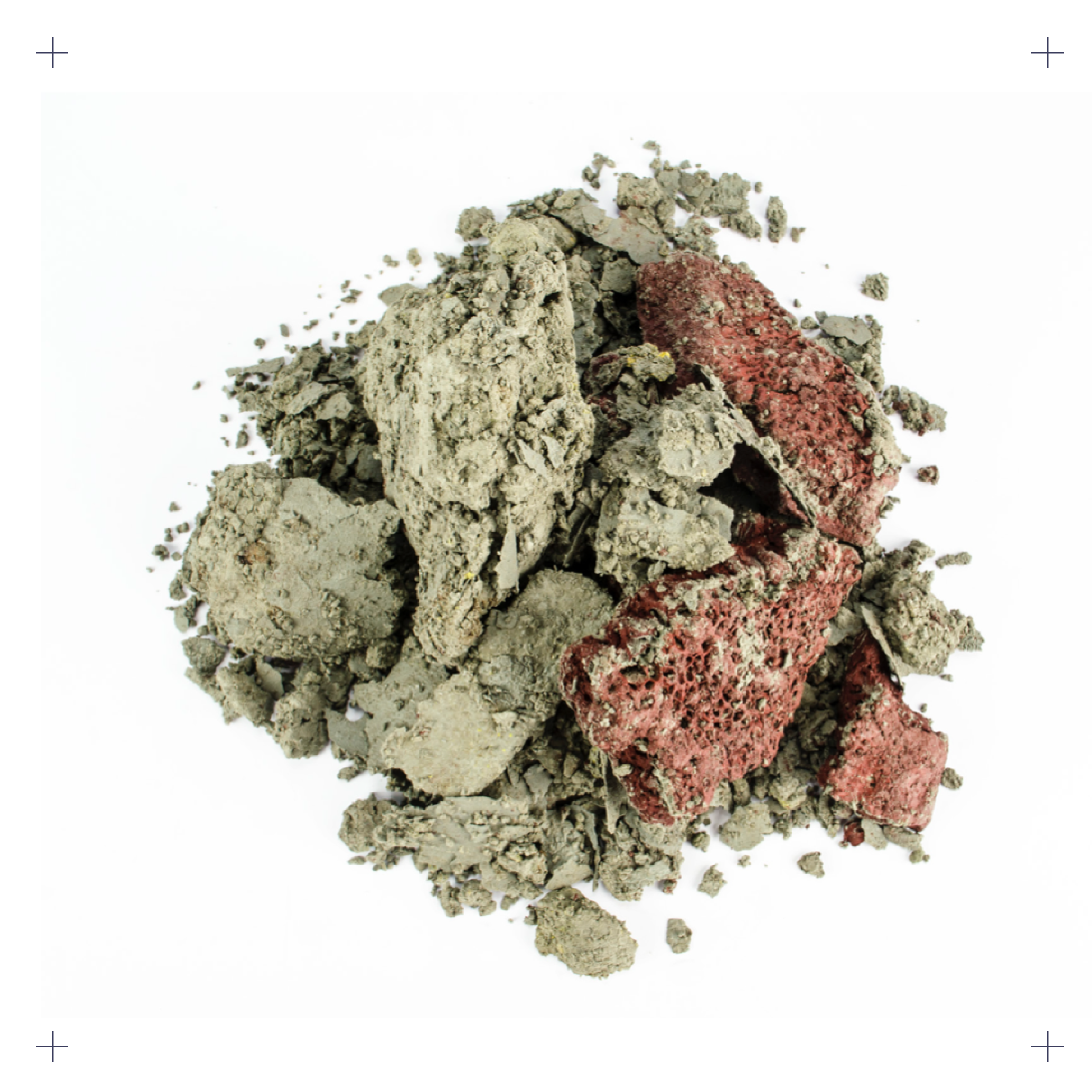


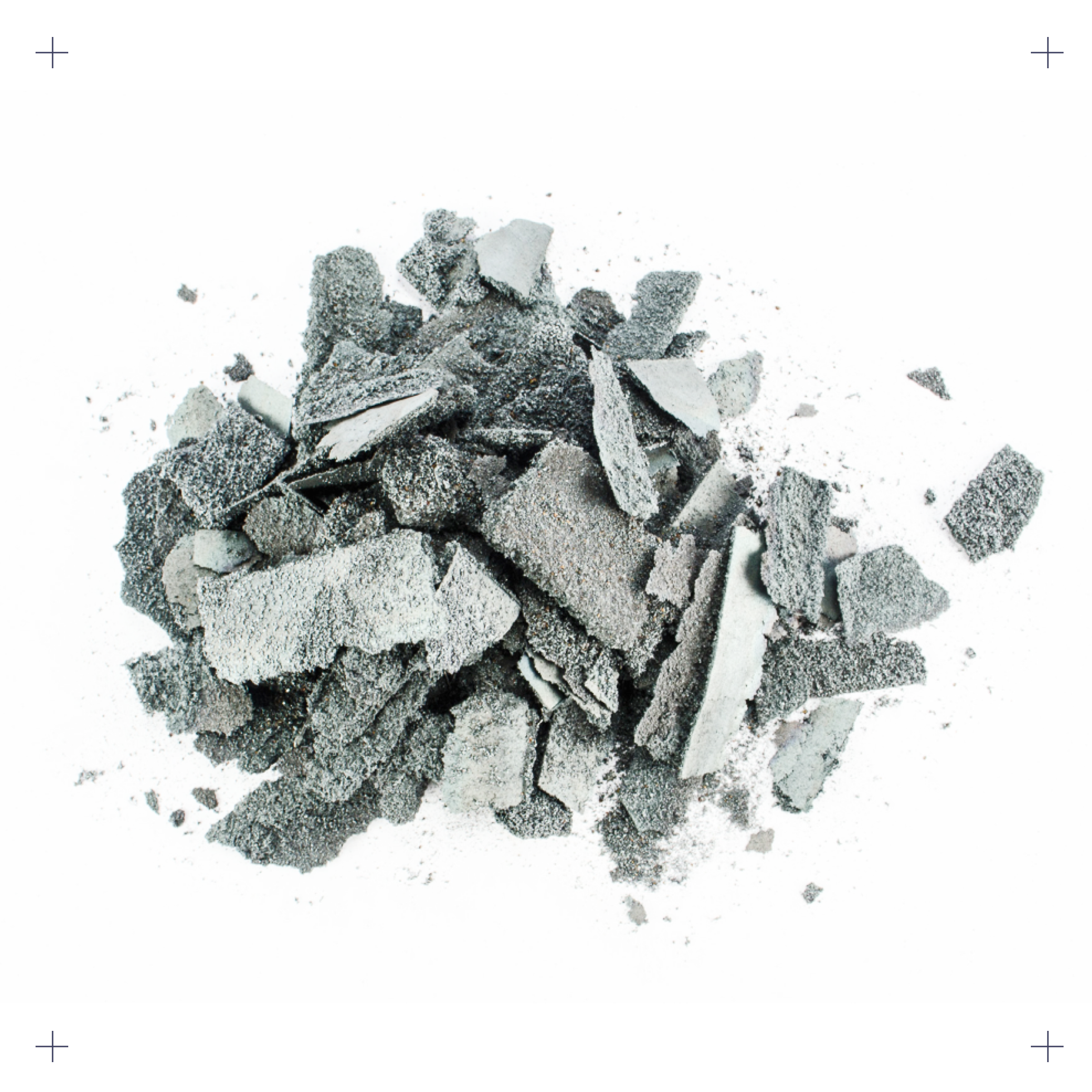
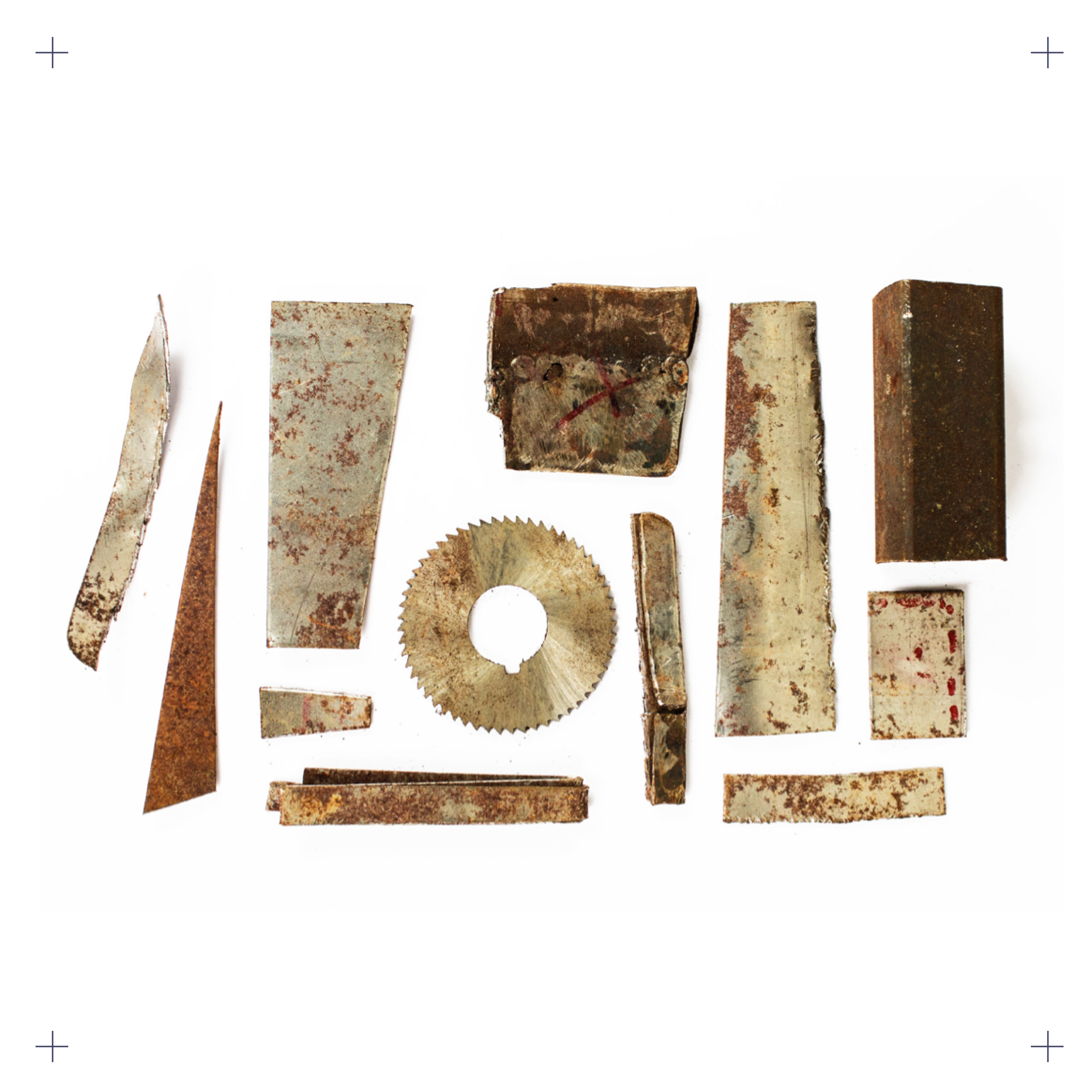
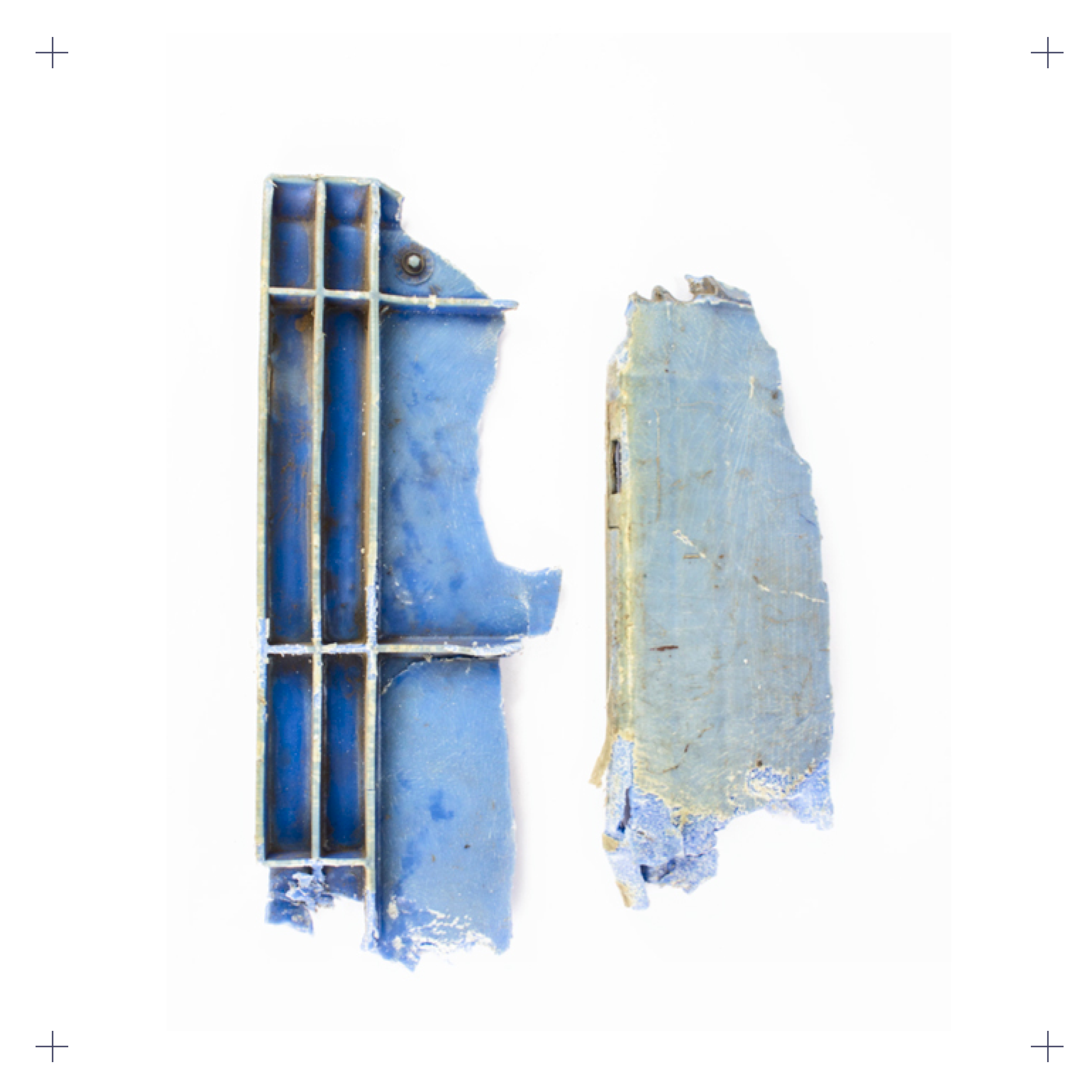
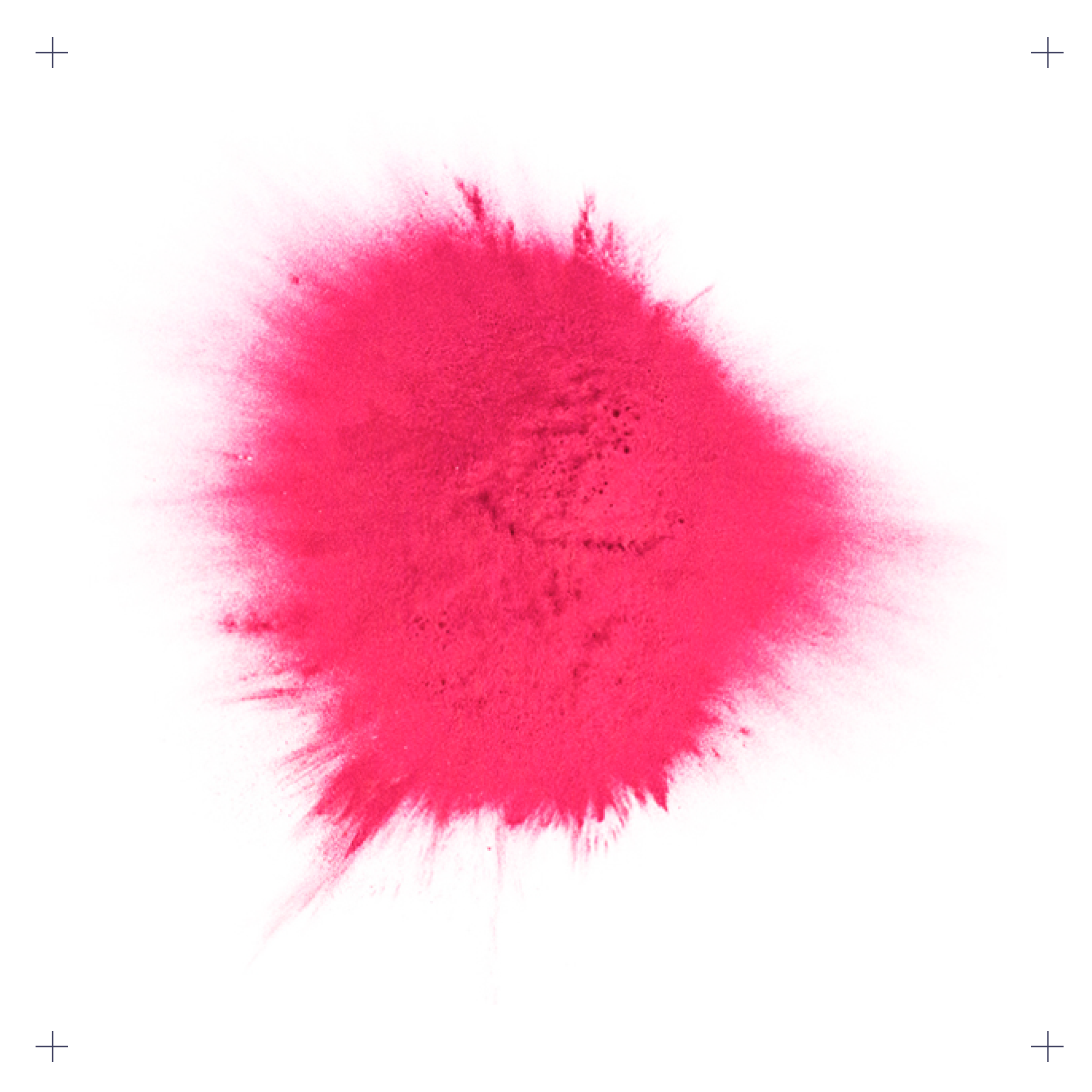
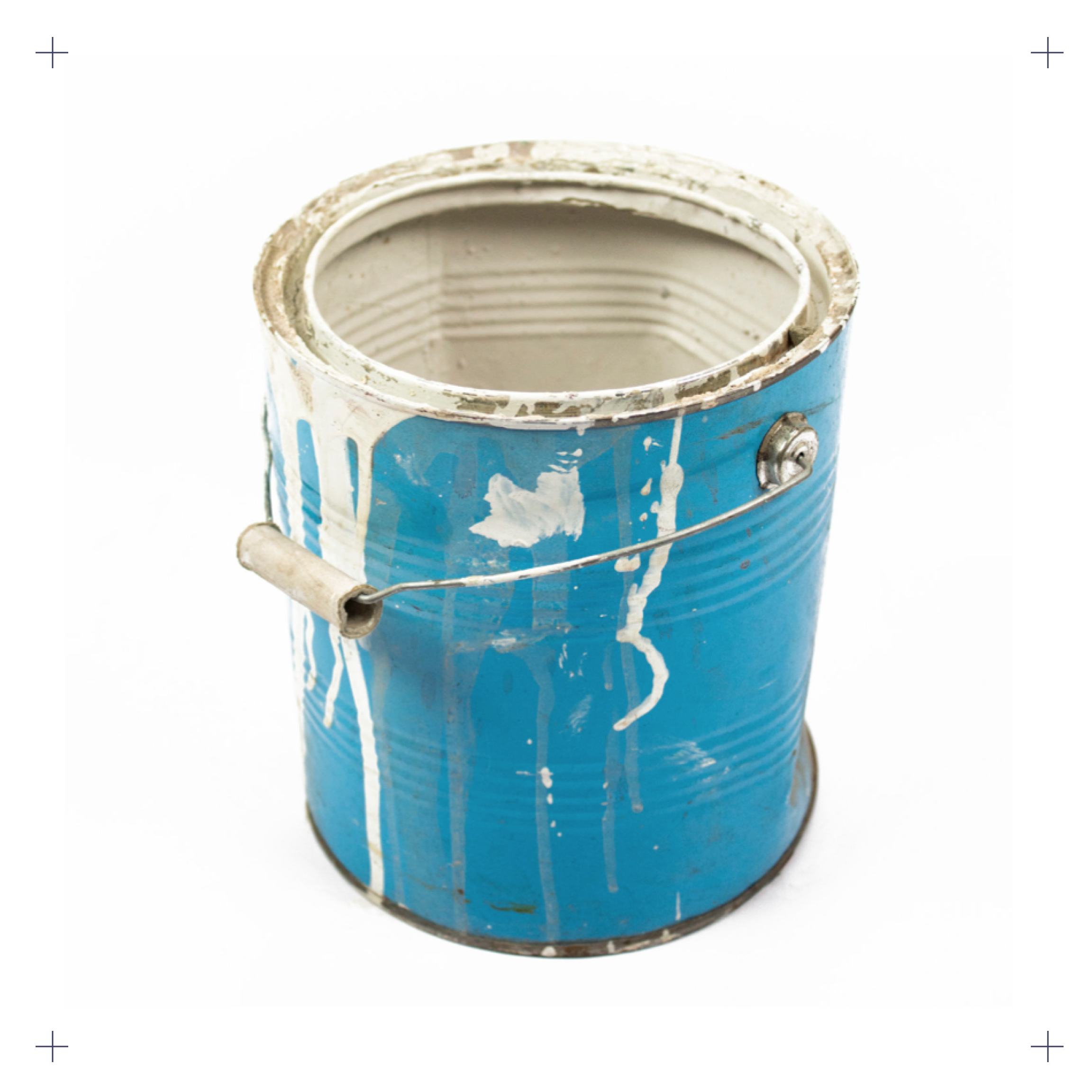

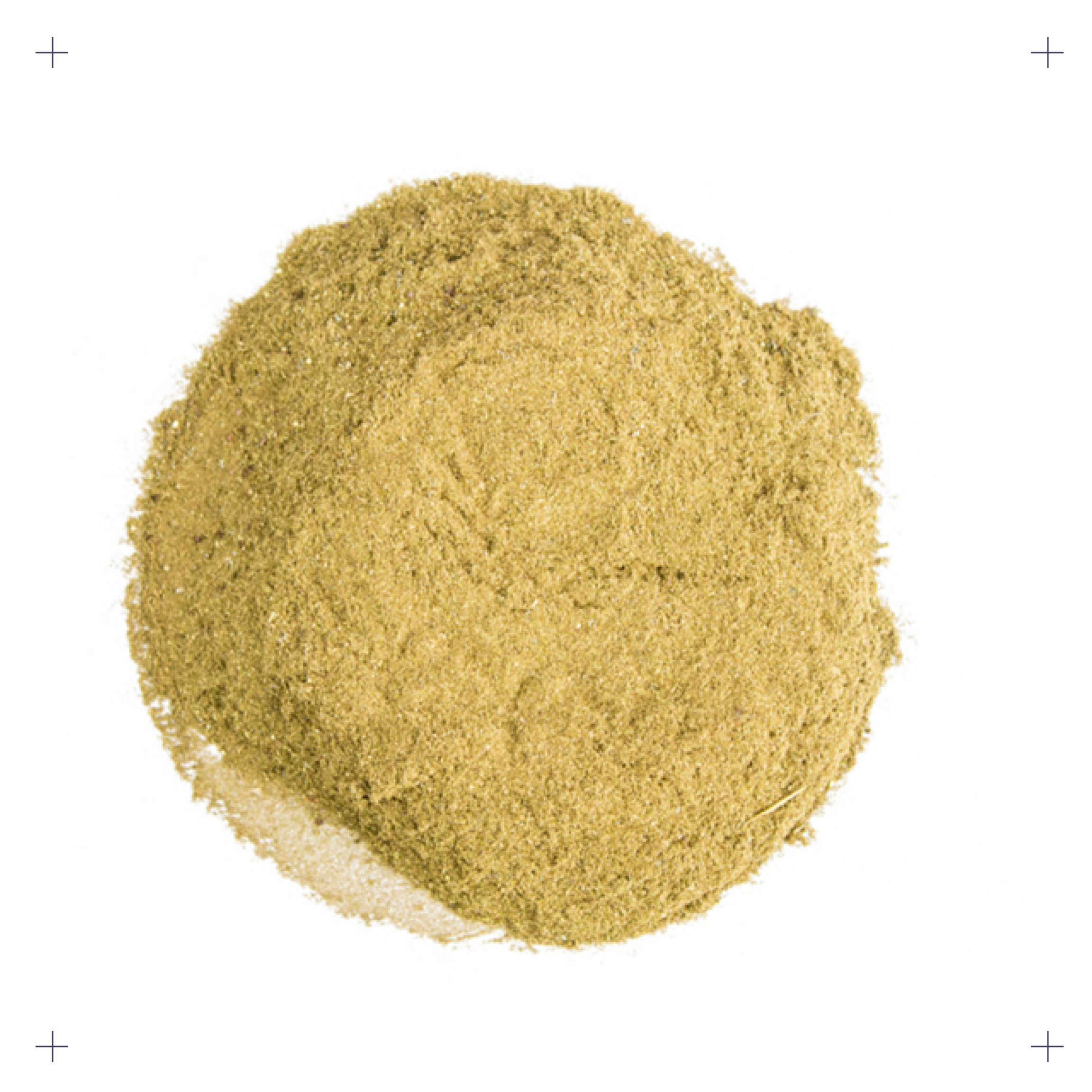

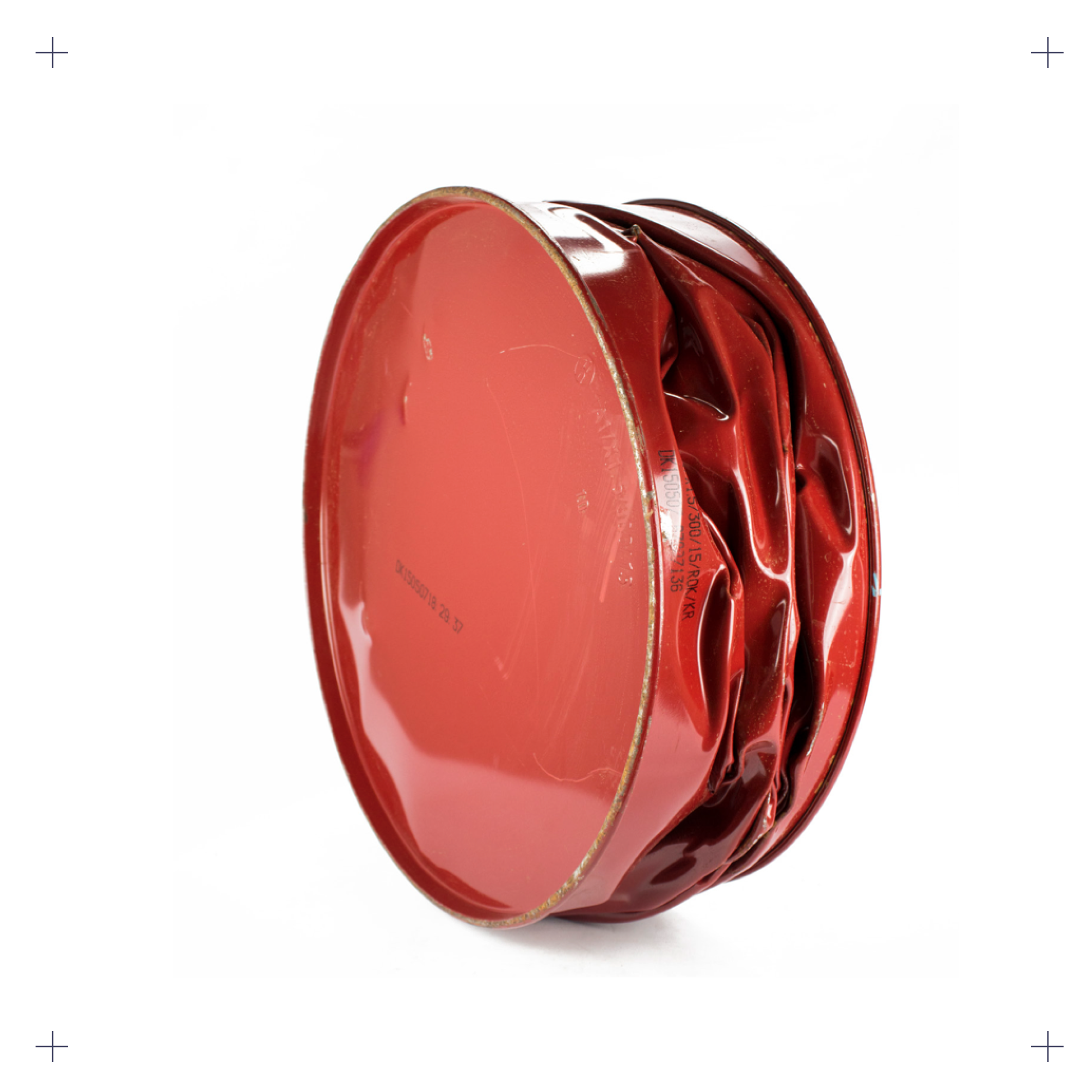

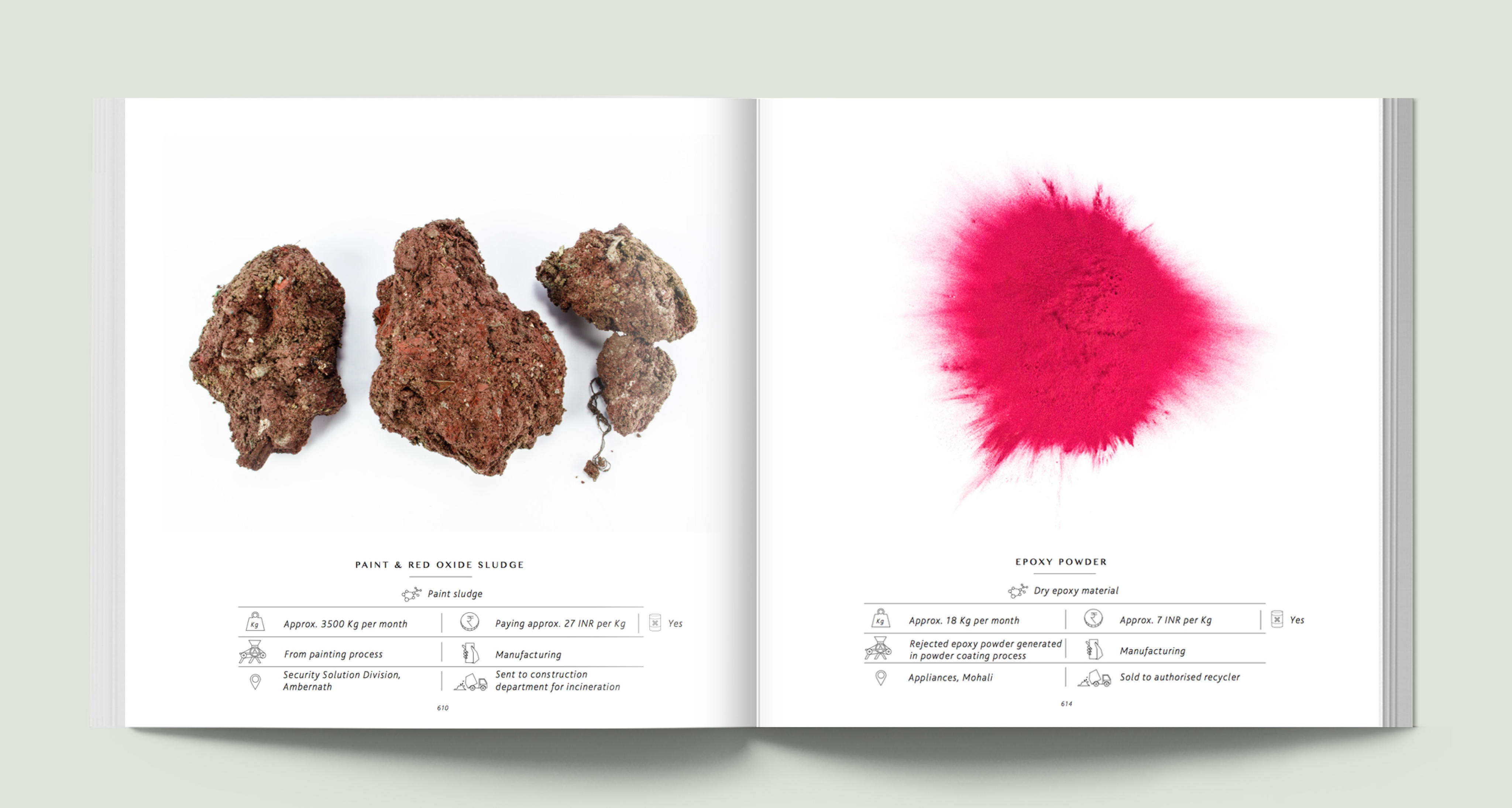
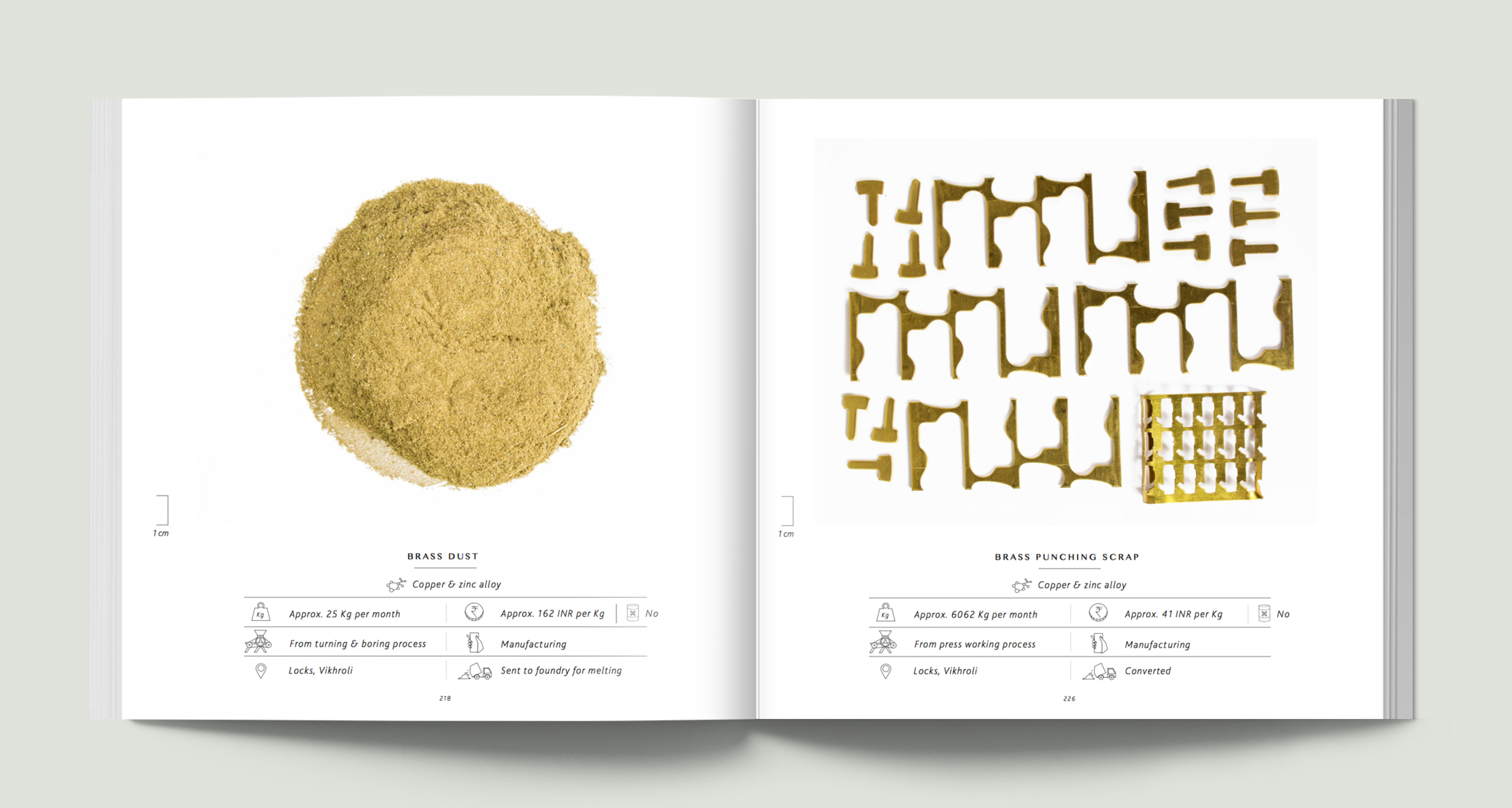


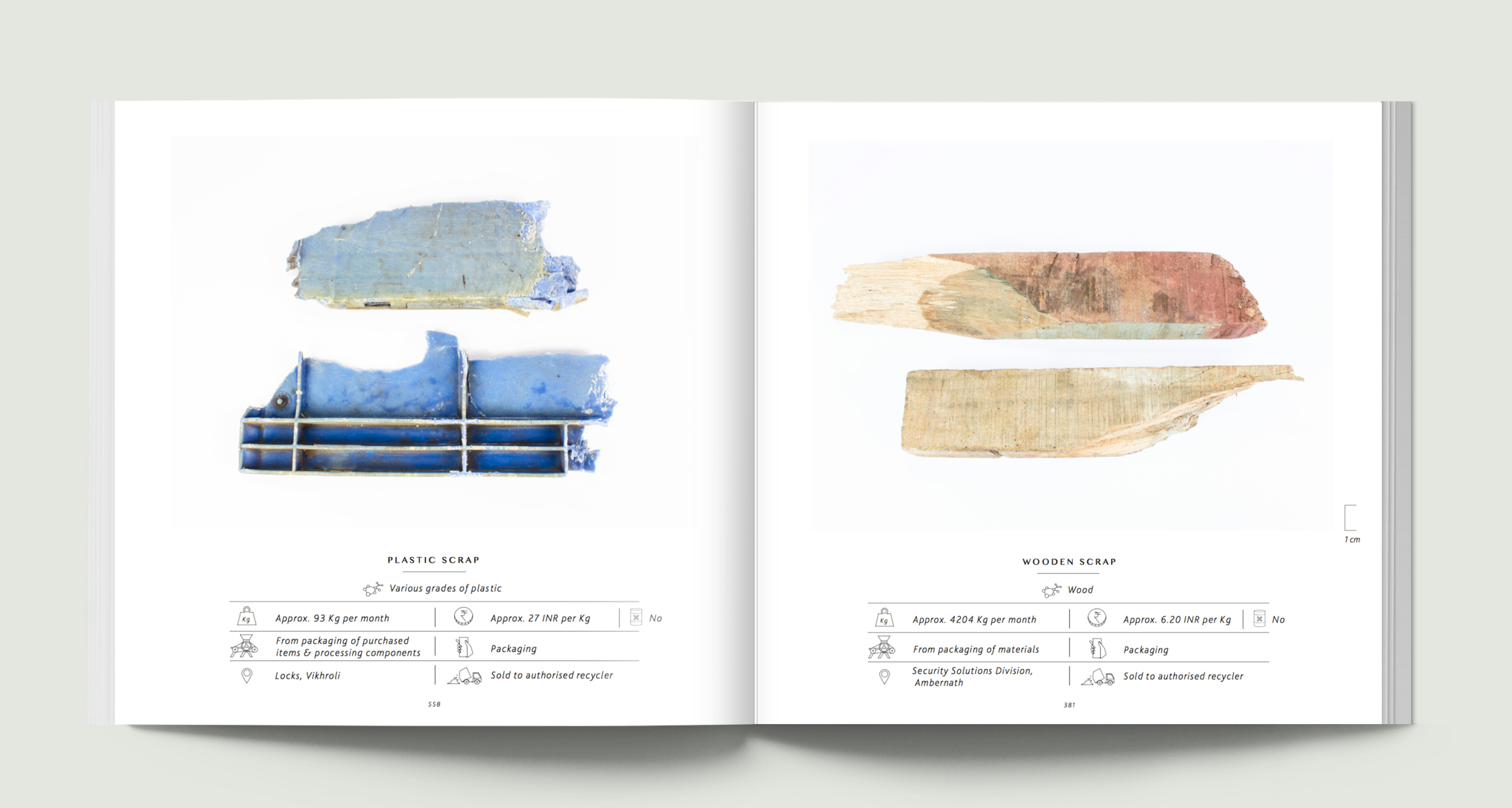
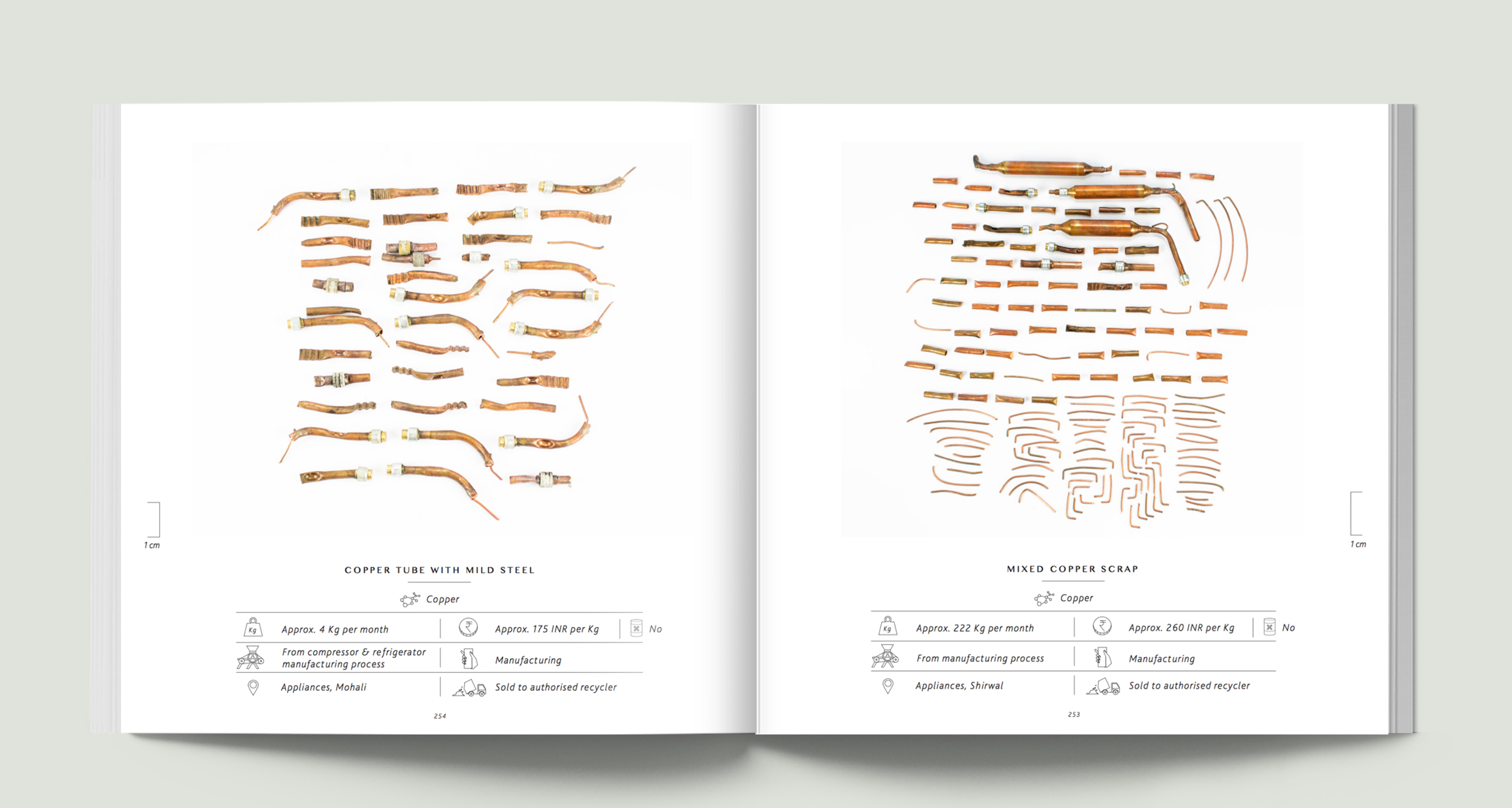
We explored materials through experimental making, taking a closer look at their natural properties and limitations
01
Materials were chosen according to the quantities generated and the environmental threat caused by sending them to incineration or landfill.
02
Through the process of experimentation, we looked for simple solutions, keeping step-processes and energy consumption to a minimum whilst looking beyond conventional boundaries.
03
We developed step processes & recycling solutions, re-introducing some of these materials back into the manufacturing process and taking into consideration what kind of usage would be most viable and scalable.
Every year 470,400 kg of turning and boring is generated.
Turning & Boring is the output of one of the most basic machining processes used to shape metal objects. This is a step-by-step guide of how to turn metal turning & boring back into solid metal to be reused.
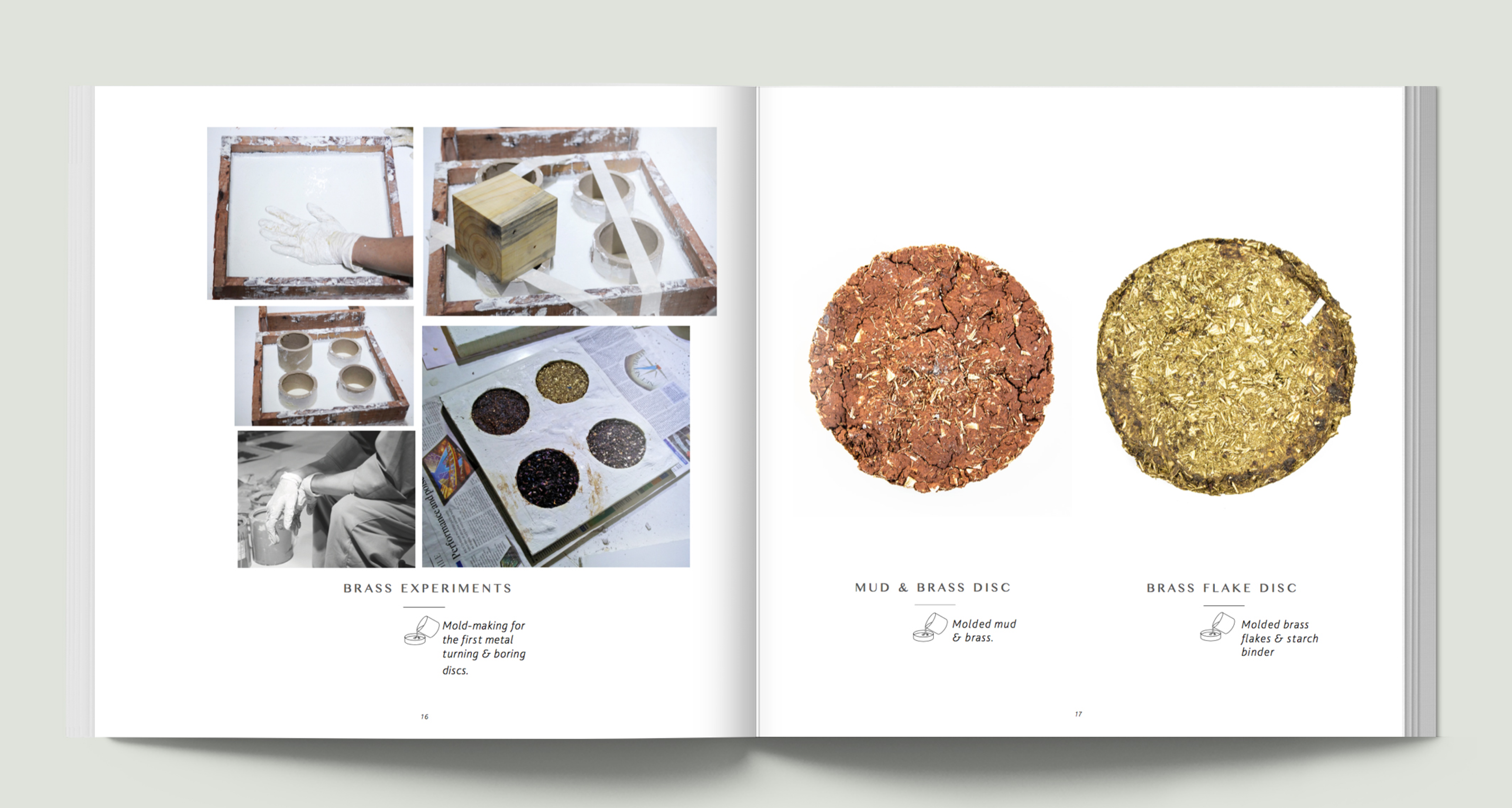








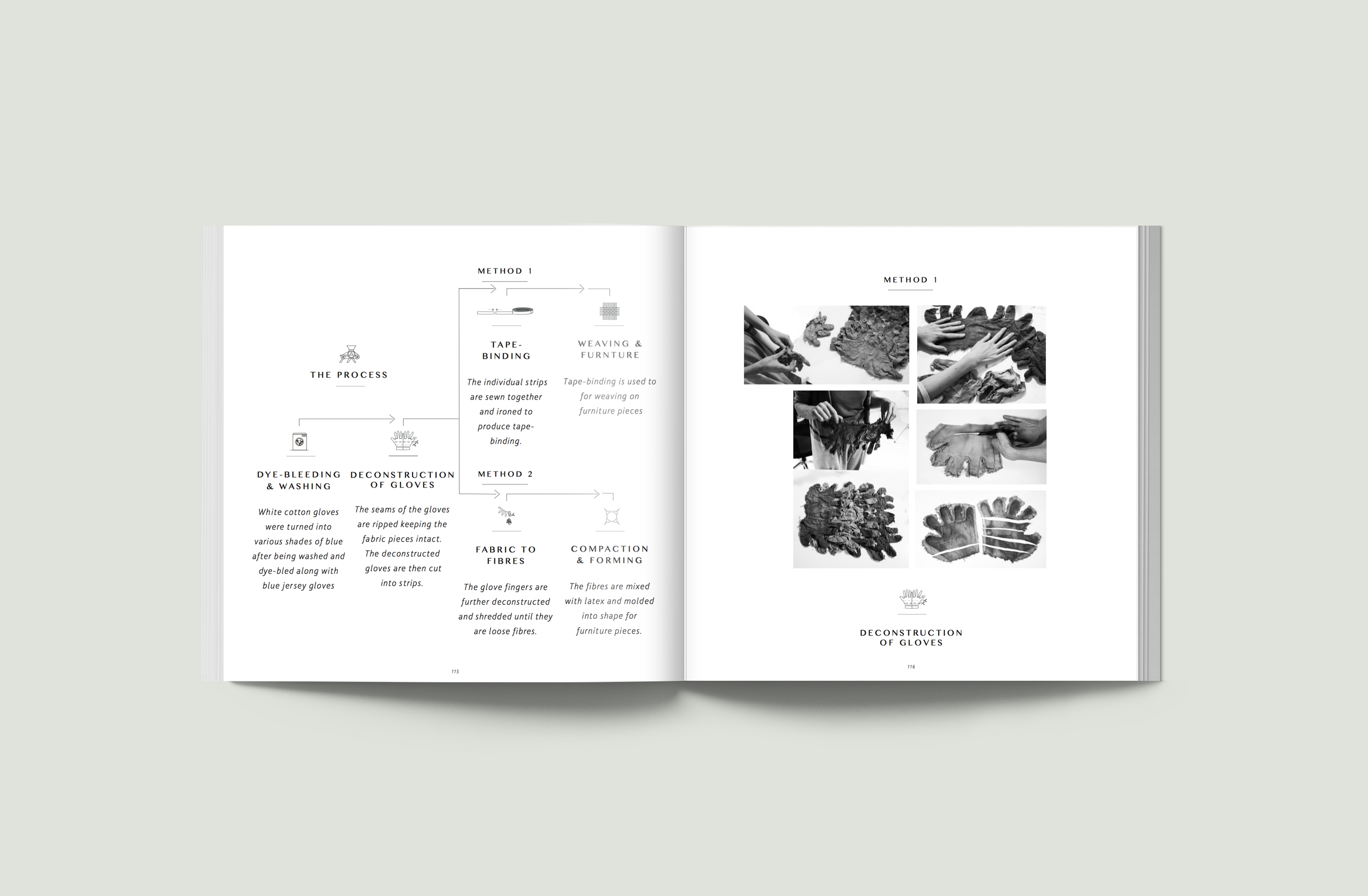

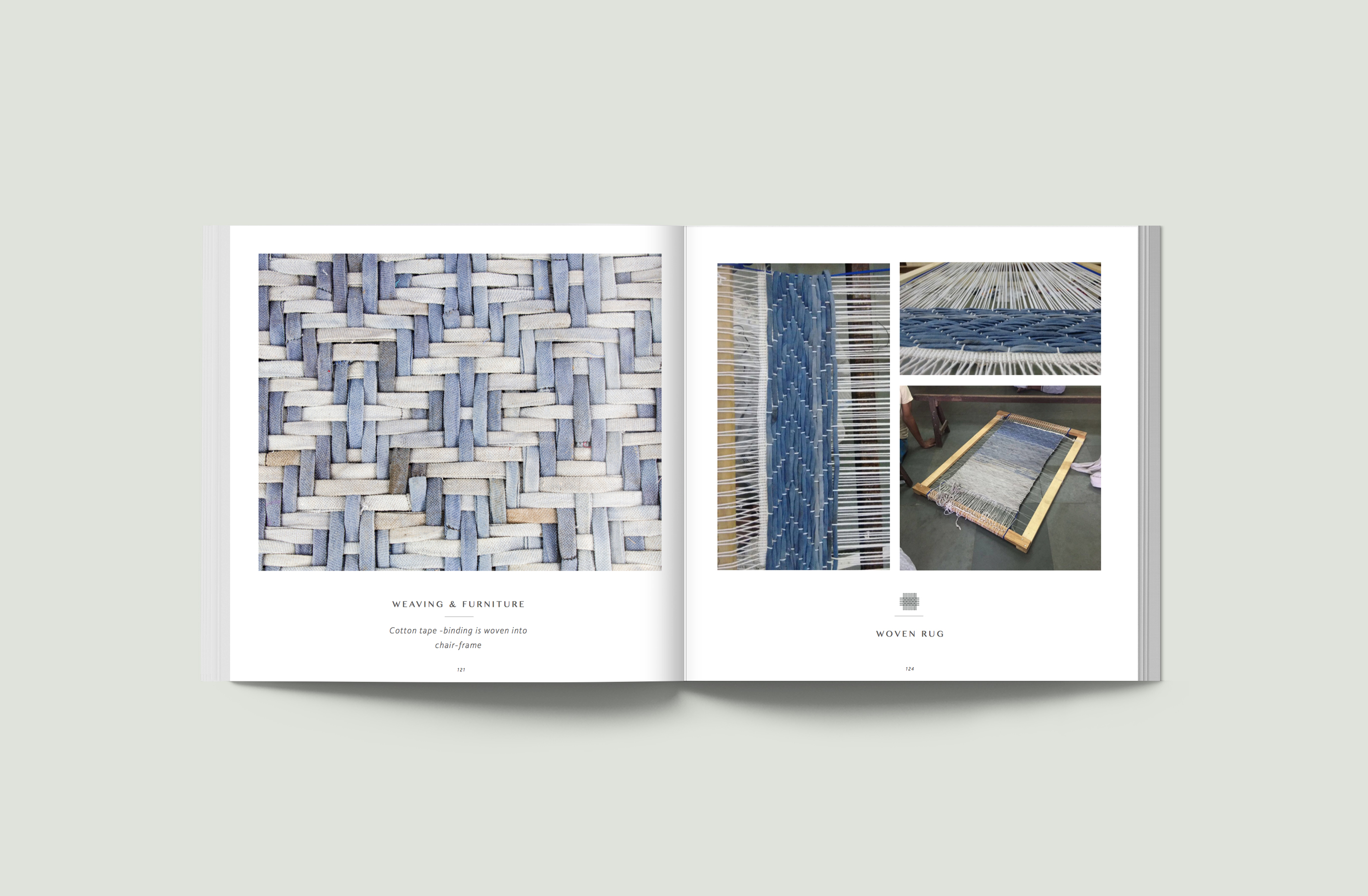

More than 15,000 pairs of gloves are discarded and collected every month from various divisions at Godrej & Boyce.
Oil soaked cotton gloves are generally sent to incineration facilities while non-oil soaked gloves are sent to landfill. Workers gloves were washed, stripped of oil and then dyed with waste dyes and upcycled into garments, rugs and upholstery.